Hallo Leute,
hier beschreibe ich mal die Technik meines aktuellen Raketengleiters inklusive Booster und Startrampe. Videos und Bilder von Flügen gibts im anderen Thread unter Multimedia.
Inhaltsverzeichnis:Einleitung
Teil 1: bodengebundene Systeme (Startrampe u.ä.)
Teil 2: primäre Flugsysteme (Antrieb, Stufentrennung)
Teil 3: sekundäre Flugsysteme (Bergung, Aerodynamik)
Einleitung Dieses Projekt (genannt: Aerodynamic Transportation System oder ATS oder Aero Shuttle) basiert sehr stark auf der Technik meiner dreistufigen Parabelflugrakete, an der ich 2004 bis 2007 gearbeitet hatte. Dazu gehören u.a. die geklebten Tanks (mit meiner Variante der verbreiteten Symmetrical Splice Technique oder SST, von mir als Direct Splice Technique oder DST bezeichnet), die Schwerkraft-/Beschleunigungs-gesteuerte Stufentrennung (Gravity Triggered Staging oder GTS), die Clustertechnik für Booster mit 20mm-Düsen mit entsprechendem Dichtsystem, 20mm-Launch-Tubes sowie ferngesteuerter Startkupplung und das ferngesteuerte Druckverteilungs- und Kontrollsystem (Pressure Distribution & Control, oder PDC) mit Startabbruch-Funktion. Im Unterschied zu damals werden jetzt viele deutlich billigere und einfacher erhältliche Teile und Materialien verwendet, aber das Prinzip ist das gleiche geblieben. Die resultierende Rakete und Startrampe ist relativ klein und leicht transportabel (statt eines vierrädrigen, geländegängigen Fahrgestells ist nun nur noch ein größerer Rucksack und zwei Hände zum Transport von Rakete und Ausrüstung notwendig).
Eckdaten des Projekts:Spannweite des Gleiters: 66,6 cm
Leergewicht des Gleiters: 840 g
(davon sind 170 g Nutzlast)
Tankvolumen des Gleiters: 1,0 l
(davon 0,5 l Wasser)
gemessene Sinkgeschwindigkeit: 3 m/s vertikal bei 10 m/s horizontaler Geschwindigkeit
Leergewicht der Booster: 830 g
(inklusive Fallschirme und GTS)
Tankvolumen der Booster: 2 x 2,4 l
(davon 2 x 1 l Wasser)
Simulierte Flugbahn (bei 6 bar Druck und vertikalem Aufstieg):
Geschwindigkeit nach Booster Cutoff: 21 m/s
Geschwindigkeit nach SECO: 33 m/s
Apogäum bei ca. 54 m
Teil 1: bodengebundene SystemeStartrampeDie Startrampe ist modular aufgebaut. Sie besteht aus einer kreuzförmigen geschweißten Stahlkonstruktion mit einem Loch oben in der Mitte, an der außen zwei oder vier Launch Tubes angeschraubt werden können. Im Moment sind es zwei - an Stelle der anderen Beiden sind Abstützungen angeschraubt.
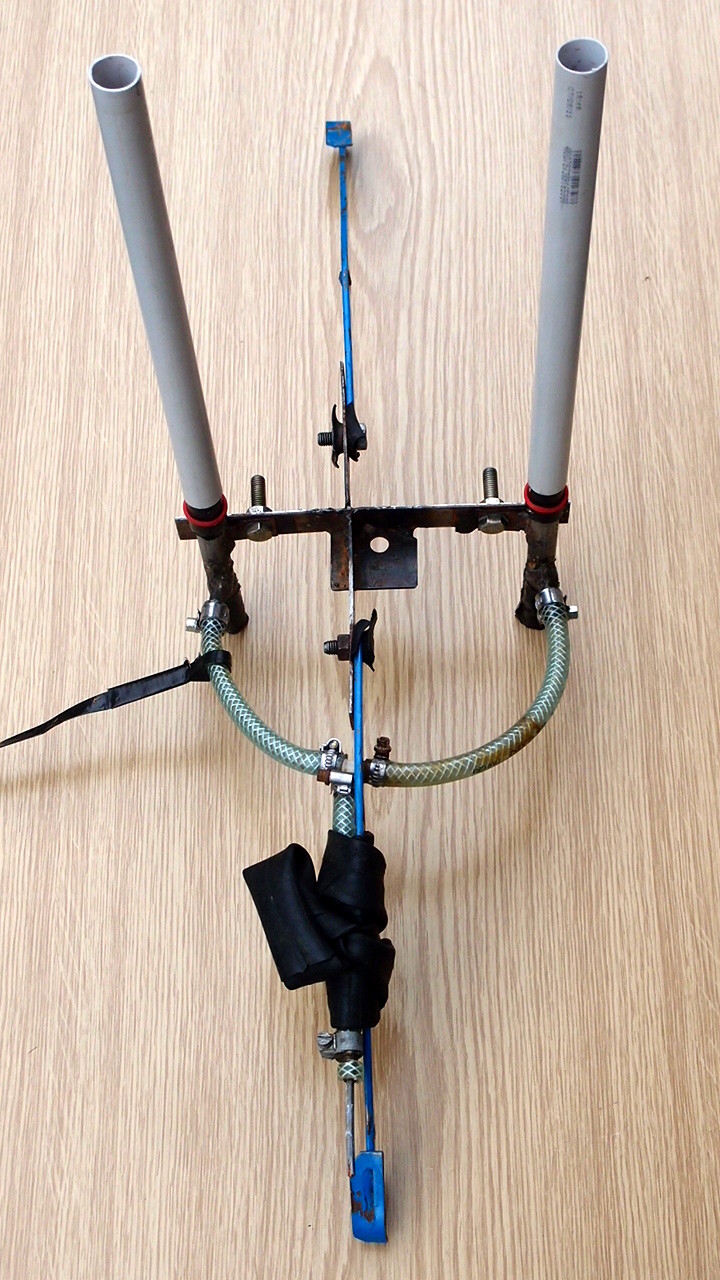
Jede Launch Tube besteht aus einem unteren kurzen 15mm-Rohr aus Stahl und einem oberen, auswechselbaren 20mm-PVC-Rohr aus Kunststoff. Das untere Ende des Stahlrohrs ist zugeschweißt und an der Seite ist ein dünneres Rohr angeschweißt, über welches ein Druckschlauch darübergeschoben und mit einer Schlauchschelle gesichert ist. Die Druckschläuche der Launch Tubes sind an einem T-Stück angeschlossen, an dessen dritten Ende der gemeinsame Schlauch angeschlossen ist, über den die ganze erste Stufe aufgepumpt wird. Ansonsten ist noch ein Blech mit nem Loch angeschweißt, sodass man die Launch Tube an die Startrampe schrauben kann.
Die Längen der Rohre sind so gewählt, dass das PVC-Rohr möglichst tief in die verwendeten Flasche der Rakete hineinragt, aber der Flaschenhals unterhalb des PVC-Rohrs das Stahlrohr umgibt. Das Stahlrohr wird mit einem geeigneten O-Ring gegen den Flaschenhals abgedichtet. Das PVC-Rohr ist gegen das Stahlrohr mit mehreren Lagen Teflon-Dichtband abgedichtet. Auf das Stahlrohr sind mehrere Lagen Duct-Tape gewickelt, sodass der verwendete O-Ring passt. Bis zur Höhe, wo etwa der Flaschenhals endet, sind zusätzliche Lagen Duct-Tape aufgewickelt um zu verhindern, dass der O-Ring assymetrisch zu weit nach unten rutscht. Da die Launch Tubes direkt auf dem Boden stehen (der oft nass, kalt, gefroren oder von Schnee bedeckt ist) ist zur thermischen Isolaton am unteren Ende noch ein Stück Holz mit Duct-Tape angeklebt.
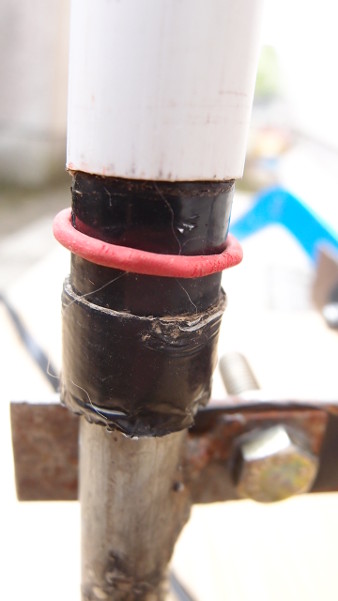
Ich verwende übrigens keine hochwertigen O-Ringe aus Gummi mehr. Stattdessen hab ich mir ne Packung Luftballons gekauft und von jedem Ballon den Rand abgeschnitten. Diesen kann man genausogut als Dichtring verwenden. Das Material ist deutlich weicher und elastischer also der typische O-Ring-Gummi, geht aber schneller kaputt.
Durch das zentrale Loch in der Startrampe wird von unten eine M8-Schraube geschoben. Sie hält die Rakete bis zum Start am Boden. Um die Schraube zum Start schnell und ohne viel Kraft aufdrehen zu können ist am Schraubenkopf ein hölzernes Riemenrad befestigt, dessen Durchmesser etwas kleiner ist als der Abstand zwischen den Launch Tubes. Auf das Riemenrad wird eine stabile Polyamid-Schnur aufgewickelt. Wenn man aus großer Entfernung beherzt an ihr zieht wird in einem Sekundenbruchteil die Schraube aufgedreht, sodass die Startkupplung entriegelt wird (High Performance Remote Unlock System oder HPRUS). Mit dieser Technik habe ich seit 2004 viele zwei- und vierstrahlige Cluster erfolgreich gestartet. Die Mutter zur Schraube ist Teil der Rakete und fliegt mit (siehe Teil 2).
Druckverteilungs- und Kontrollsystem (PDC)Um die Druckluft von der Pumpe in die verschiedenen Tanks der Raketenstufen zu leiten wird ein System von Druckschläuchen, Fahrrad- und Auto-Ventilen und schnell lösbaren Druckluft-Verbindungen verwendet.
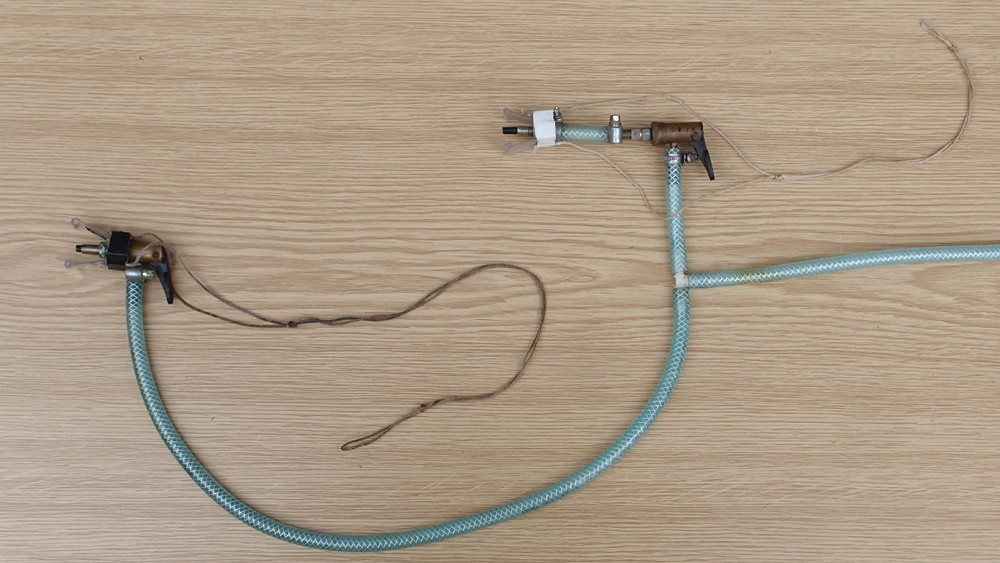
Von der Pumpe ausgehend führt erst ein ca. 10 m langer Schlauch bis kurz vor die Startrampe. Über ein T-Stück sind dann zwei Schläuche angeschlossen: einer führt direkt zur Druckluft-Verbindung der zweiten Stufe, der andere zunächst zu einem Einweg-Ventil und danach zur Druckluft-Verbindung der ersten Stufe.
Das Einweg-Ventil ist ein Fahrradventil (Blitz-Ventil), auf welches ein Ventiladapter für Autoventil-Anschlüsse geschraubt wurde, sodass man dort einen Schlauch oder einen normalen Ventil-Anschluss anbringen kann. Das Ventil ist so herum eingebaut, dass es schließt, wenn der Druck in der ersten Stufe größer ist als auf der Seite, die dem T-Stück zur zweiten Stufe zugewand ist, und andernfalls öffnet.
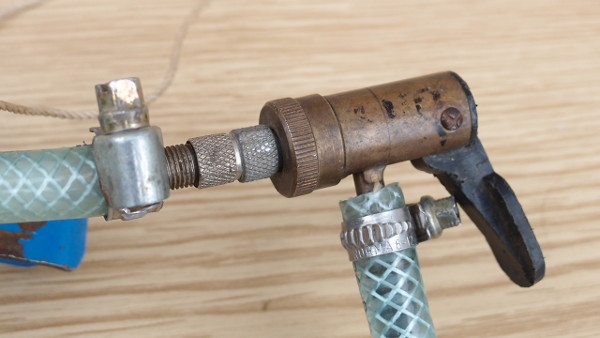
Die schnell lösbaren Druckluft-Verbindungen hab ich letztes Jahr entwickelt. Eine Verbindung besteht aus zwei abgesägten Fahrrad-/Autoventil-Schäften, die aufeinander gepresst werden und über eine innen hineingesteckte rohrförmige Dichtung verbunden und abgedichtet werden. Die Dichtung besteht aus einem Stück eines Kunststoff-Trinkhalms mit einer Lage Duct-Tape darüber. Damit die Dichtung beim Aufeinanderpressen nicht einknickt oder Falten bildet wird innen noch ein Stahlstift hinein gesteckt, der gerade so in die Dichtung hinein passt. In den Stift wurde eine Längsnut gesägt, um die Druckluft durchzulassen. Wenn das Gegenstück der Druckluft-Verbindung ein Autoventil ist - wie im Falle der Verbindung zur zweiten Stufe - dient der Stift auch dazu, das Ventil offen zu halten, bis die Verbindung gelöst wird. Der Anpressdruck wird von einer Klammer aufgebracht, die aus einem Stück PET gefertigt wurde (durch Erhitzung mit einem Bügeleisen). Auf beide Ventilschäfte ist jeweils ein kurzes Stück Schlauch geschoben. Die PET-Klammer umgreift mit beiden Enden das eine Stück während sie mittig auf das andere Stück drückt. Um die Klammer geschlossen zu halten ist sie von einem Vierkantrohrstück umgeben, das ebenfalls aus PET geformt wurde und mit Duct-Tape zusammengehalten wird. Es ist an gegenüberliegenden Seiten mit einer stabilen Schnur verbunden. Wenn man an der Schnur zieht, kann man schnell und mit wenig Kraft die Verbindung lösen. Bei Bodentests stellten sich diese Verbindungen als ausreichend dicht bis 7 bar heraus, aber im Flugbetrieb gab es gelegentlich schon deutliche Lecks ab 4 bar, wenn die Länge der Dichtung nicht genau stimmte und der Anpressdruck zu niedrig war. Letzterer ist einstellbar über die Position der Schlauchstücke auf den Ventilschäften und Erstere ist einstellbar mithilfe einer Schere oder mit Ersatz-Dichtungen, die zumindest schnell hergestellt sind und fast nix kosten.
Normaler StartablaufVor dem Start werden zunächst alle Tanks gleichzeitig aufgepumpt. Wenn der vorgesehene Flugdruck erreicht wurde muss mit einem ferngesteuerten Kommando der Versorgungsschlauch der zweiten Stufe (Kernstufe, in dem Fall: der Gleiter) abgetrennt werden (Core Umbilical Retraction oder CUR). Dadurch fällt der Druck im Schlauch schlagartig ab. Um zu verhindern, dass dadurch die erste Stufe Druck verliert muss das Einweg-Ventil vor der ersten Stufe geschlossen werden. Das geschieht automatisch und schnell genug durch den Druckabfall im Schlauch. Danach sollte der Druck in allen Raketenstufen konstant bleiben. Nun kann das Kommando zum Start (Unlock) gegeben werden. CUR und Unlock müssen möglichst schnell aufeinander folgen, da in dieser Zeit nur ein eingeschränkter Startabbruch möglich ist (siehe unten).
StartabbruchIndem die Druckluft-Verbindung zwischen dem Einweg-Ventil und dem Schlauch zur ersten Stufe getrennt wird, wird der Druck aus allen Tanks der ersten Stufe abgelassen (Abort). Solange die Verbindung zur zweiten Stufe noch besteht und das Einweg-Ventil offen ist wird durch diese Maßnahme ebenfalls der Druck aus der zweiten Stufe abgelassen. Das Abort-Kommando sollte also möglichst vor dem CUR-Kommando gegeben werden, da sonst der Druck der zweiten Stufe nur durch Auslösung der Stufentrennung bzw. des Starts (oder Fehlstarts) abgelassen werden könnte. Wenn der Grund für den Startabbruch ein Dichtigkeitsproblem in einer beliebigen Stufe ist und CUR noch nicht durchgeführt wurde, ist das Abort-Kommando nicht zwingend notwendig, da aus dem Leck mit der Zeit der Druck aus allen Tanks entweicht (Auto-Abort). Das ist möglich, weil das verwendete Einweg-Ventil erst ab einem bestimmten Druckunterschied schließt.
Remote Control Lines (RCLs)Es gibt drei ferngesteuerte Kommandos, die durch Ziehen an je einer Schnur (sog. RCL) aus 10 Meter Entfernung gegeben werden: Abort, CUR und Unlock. Es werden sehr stabile Schnüre aus Polyamid verwendet, die im Baumarkt erhältlich sind.
Geändert von TR260 am 17. Mai 2016 um 02:55